Once again the team at Centriblast provide a problem solving Automatic Blast Machine solution for another leading UK manufacturer!
Our customer required a solution to increase their manufacturing output of concrete slabs, whilst also providing an energy efficient solution. Our expert engineers worked hand-in-hand with our customer to fully understand their in-house process, to ensure the best possible solution to meet their exact requirements was provided.
Installation: Concrete Slab Etch Blast Machine
Centriblast design, manufacture, deliver and install all Automatic Blast Machines we supply. Once delivery of the Concrete Etch was successfully completed our installation team began the install.
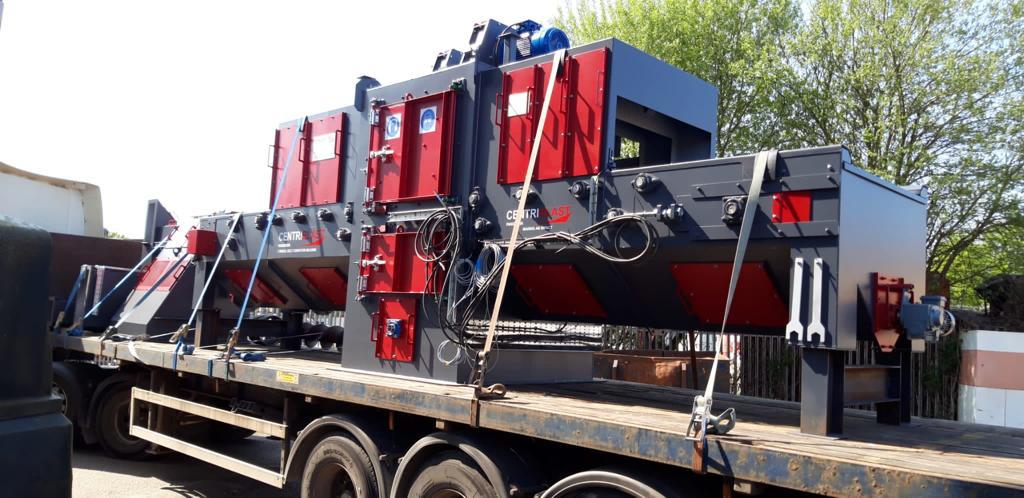
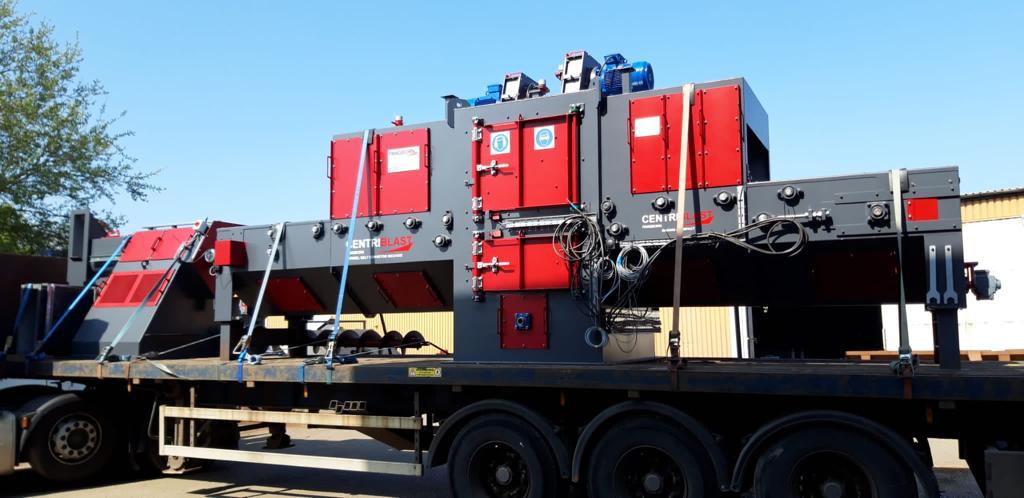
Technical Specification
The machine is designed to blast the following range of components:
- Slabs
- Curbs
- Edging
Conveyor Belt Details;
- Maximum belt width – 1050mm
- Maximum component width – 900mm
- Maximum component height – 300mm
- The maximum weight of component is 150kg per metre.
There is no minimum component length as such but the limiting factor is normally the weight of the component – light components can move around on the belt resulting in poor blasting.
Suggested Blasting Media
The softest possible blasting media should always be used in order to achieve the lowest possible operating costs.
The total quantity required for the initial commissioning of the machine is 3 tonnes and the exact size is dependent upon the makeup and hardness of the concrete products and the desired surface finish after blasting.
Standards of Finish
The machine is designed to blast the specified range of concrete components and to achieve a variety of finishes by varying a number of parameters including the amount of abrasive being thrown by the wheel units, the size of the abrasive, the conveyor speed and also in some cases the rotational speed of the blast wheels.
Typical throughput speeds depending on the above parameters and also the age of the
concrete product are as follows;
15 KW blast wheels are fitted then the conveyor speed required will be between 1.0 and 3.0 metres per minute.
Larger wheel motors can also be fitted.
Pangborn ACU-STRIKE ROTOBLAST® Wheels
Wheel blades are cast in carbon chromium molybdenum alloy steel using a state of the art lost foam casting process and heat treated in an inert gas batch furnace. Blade life can be in excess of 1700 hours and wheel life 3000 hours to 6000 hours’ subject to the use of a good quality steel shot of hardness 45 – 53 RC
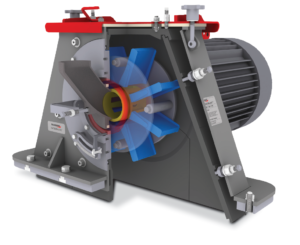
and also dependent on wheel motor size and speed.
The wheels have the following advantages;
- Lower power consumption and quieter running than other makes of blast wheel
- Very simple blade changing and “user friendly” flange mounted wheel motors
- Non-handed reversible wheels and blades with very long life
- Designed to operate from 2000 to 3800rpm with inverter control
Also fitted with this machine;
- Blast Cabinet and Recovery Hopper
Centriblast – Concrete Slab And Kerb Etch Machine - Belt and Bucket Elevator
- Pangborn Separator Unit with Variable Speed Rotary Sieve
- Pangborn Separator Unit with Variable Speed Rotary Sieve
- Rotary Sieve
- Platform and Ladder
- Inlet and Exit Vestibules
- Abrasive Removal Blower
- Heavy Duty Conveyor Belt; working conveyor with = 1000mm / conveyor load capacity of; 150kg/m
- Pangborn Cartridge Type Pulse Jet Dust Arrester
- Filter Cartridges
- Fan System
- Disposal of Collected Dust
- Dust Collection
- Efficiency Levels and current COSSH and EPA Regulations
- Disposal of Collected Dust
- Cyclone Unit
- Connecting Ductwork
- Machine High Quality Paint Finish
- Electrical Control Panel
- Control and Information Display Centre
- Electrical Wiring
Centriblast – Concrete Slab And Kerb Etch Machine
List of Electric Motors
- Wheel units x 3 @ 15.0 KW
- Elevator and main screw conveyor x 1 @ 3.0 KW
- Rotary sieve x 1 @ 1.5 KW
- Inlet screw conveyor x 1 @ 0.75 KW
- Outlet screw conveyor x 1 @ 1.1 KW
- Dust arrester {13600 m3/h) x 1 @ 15.0 KW
- Belt conveyor variable speed x 1 @ 1.5 KW
- Blower fan x 1 @ 11.0 KW
Centriblast Concrete Slab Etch Machine – Installation
Return on Investment…
Due to the new installation of the automatic concrete etch machine, our customer has seen a drastic improvement in productivity, and profitability.
- Better Output Production
- Reduced Environmental Impact
- Increased Energy Efficiency
✔️ Triple ROI due to 3 x more output production.
The new installation has reduced the company’s environmental impact, with a reduction in their carbon footprint. This has been mainly achieved due to full replacement of an old inefficient blast system. Upgrading to a new, efficient and environmentally friendly system.
The environmental impact of our customer, is further reduced with the new machine, due to the industry leading Air Wash Separating Unit. Designed to recycle waste created from etching the concrete slabs, back into the machine.
More Details
If you’d like more details on the Centriblast Concrete Slab Etch Blast Machine, or to discuss upgrading your current automatic blast equipment. Contact Centriblast-Pangborn on – 01352 712 412, or email us at – info@centriblast.com.